Table of Contents
1. Comparing Motor Types, Features, Construction and Control Methods
In our everyday life, we come across a wide variety of motors.
The following describes mainly DC motors (powered by direct current), which are easy to control using microcontrollers or controller ICs.
2. Brushed DC Motors
Because of the later introduction of brushless DC motors (BLDC motors), the earlier type of DC motor then became known as a brushed DC motor.
A stator with a pair of S-pole and N-pole magnets are part of the housing. The rotor consists of the coils and the commutators and is located inside the stator. The rotor rotates along with the current that is passed from the fixed brushes to the commutators connected to the coils.
As the motor construction is relatively simple and it is easy to drive and control, it has found use in many applications.
In a brushed DC motor, rotation speed and direction are controlled by changing the voltage input to the motor.
During rotation, the repeated intermittent contact and non-contact between the brushes and the commutator, which form the current path, generate electrical and mechanical noise. As brushes wear out, periodic maintenance is required.
3. Stepping Motors
In a stepping motor, pulse signals are input to the stator coils to cause a rotor consisting of a permanent magnet or soft magnetic material to rotate at step angles.
Stepping motors with a permanent magnet rotor are called a PM (Permanent Magnet) motor and can maintain an angle at high torque without using any power.
Stepping motors with a soft magnetic material rotor are called an SR (Switched Reluctance) motor and cost less than a PM motor, but are not as efficient.
An SR motor conducts current to the coils opposite the stator to attract the pole of the rotor and thereby turn the rotor step by step.
This motor has two drawbacks. Its drive circuit is overly large because each stator coil requires its own drive circuit and is prone to mechanical noise as each step is driven.
4. BLDC Motors
In a BLDC motor, a brushless DC motor, there is a rotor with permanent magnets and the stator whose coils create the magnetic fields that rotate the rotor.
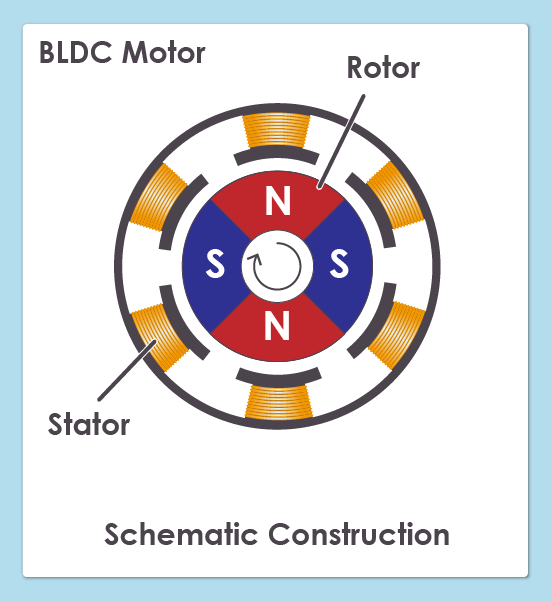
These parts replace the stator and rotor of a brushed DC motor while a control circuit electrically replaces the brushes and the commutator, which are the weaknesses of a brushed motor.
These changes improve the efficiency of the motor guaranteeing long life and low noise.
The current in the stator coil must be controlled to ensure that the rotor rotates correctly. The controller in a BLDC motor uses a position sensor to detect rotor rotation position and control the current supplied to the coil.
For more information, please refer to "What is a BLDC motor?".
5. Motor Comparison
The features of these different DC motors can be summed up as follows.
Different applications require a different DC motor.
For example, a stepping motor would be ideal for applications where the motor must be frequently stopped at a variety of angles. The BLDC motor is suited to operations that require energy efficiency and continuous operation. The brushed DC motor is good for low frequency and low-cost operations.
Brushed DC Motors | Stepping Motors | BLDC Motors (Brushless DC Motors) |
|
---|---|---|---|
Service Life | Short | Long | Long |
Electromagnetic Noise | High | Relatively low | Low |
Vibrations | Relatively small | Relatively large | Small |
Static Accuracy | Low | High | Relatively low |
Max. RPM | Relatively slow | Relatively fast | Fast |
Energy Efficiency | Relatively low | Low | High |